Teknikum
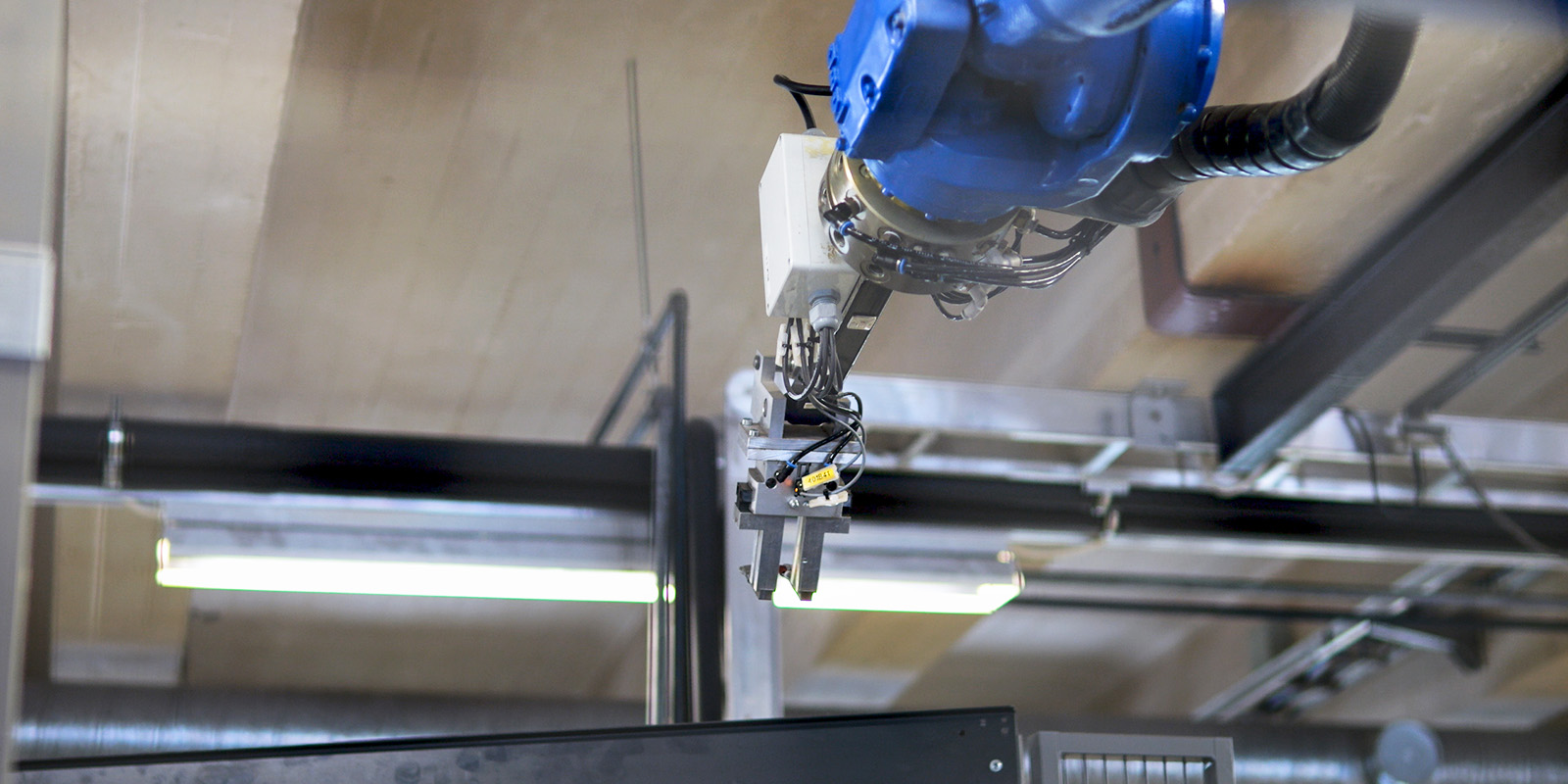
Teknikum, an industrial company operating internationally, adopted Microsoft Dynamics 365 solution, which enables an intelligent and real-time view of the entire global operation. There has been a close collaboration between Teknikum and Fellowmind for several years.
Teknikum has over three decades of experience in manufacturing and product development of rubber, plastic, silicone, polyurethane and foam products. The products are used in demanding industries for material transfer as well as for protecting processes and equipment from corrosion and wear. Teknikum Group, which employs 530 people, is a pioneer in its field in sustainable development and safe, long-lasting solutions.
The company, which operates in Europe, has an extensive reseller network and production in Finland and Hungary. Teknikum emphasizes the importance of innovation and efficiency in all its operations.
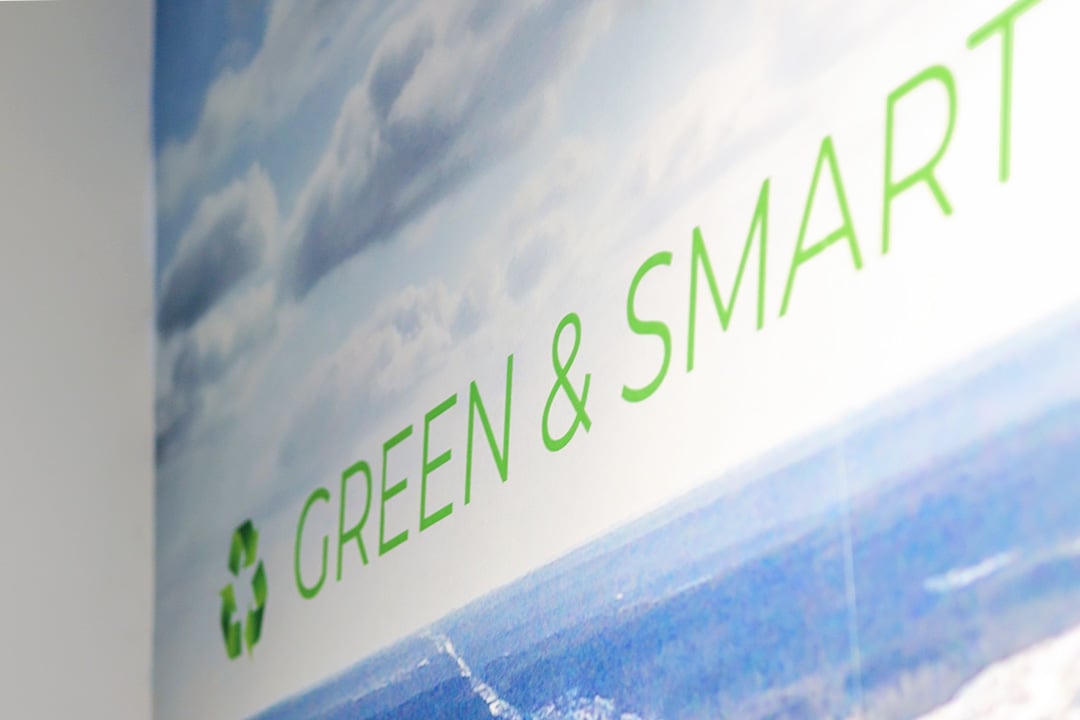
Intelligent and real-time view for managing global operations
The long-term partnership with Fellowmind covers financial operations, supply chain management (SCM) and customer relationship management (CRM). The chosen technology solution is Microsoft Dynamics 365, and the goal is to achieve a high degree of digitalization of all functions.
“We are a trusted partner for our long-term customers, and we want to develop our technical leadership by digitalizing the entire production and supply chain,” says Matti Hulmi, ICT Manager of Teknikum, who was responsible for the project.
One of Teknikum's core values is looking to the future and being responsible. A growing company that invests in the latest work methods attracts skilled employees and encourages a customer-centric approach. That is why the cooperation with Fellowmind has not been just an IT project, but a development of the company's operations.
For Teknikum, it is important to pay attention to their employees by continuously developing the work environment and systems — this way everyone can feel proud of their own company and its processes.
Fellowmind x Teknikum
Polymer Technology Solutions for International Markets
Customer companies use Teknikum's industrial hoses, moulded products, rubber compounds, rubber coatings and polyurethane and liquid silicone products in demanding applications. High-quality products, contract manufacturing services, customer-specific customization, and service solutions that support the customer's process involve significant customer-specific design and precise management of the entire operation. Customers operate in different sectors and the product range is wide. This has brought complexity to the company's processes over the years.
Customer service capability requires manageability and transparency in such conditions. Teknikum assessed that the previous IT systems would no longer be able to scale to the needs of the growing business, and a solution built from several different systems would not provide the best conditions for streamlining processes. The time was ripe for a comprehensive reform.
Challenges
Teknikum had several separate systems and a fragmented visibility of global operations resulting from rapid growth. The goal was to streamline operations and increase efficiency. Well-serving, but scattered systems did not form a strong digital foundation for the company's future growth.
The objective was clear: to streamline processes, improve visibility into all operational activities, and create a unified digital business platform that enables future growth and new businesses. At the same time, it would facilitate the management of sustainability initiatives and responsible practices.
A key improvement was desired in supply chain transparency and service capability. The new solution needed to enable the extensive and up-to-date utilization of data across the entire chain: production, sales, deliveries, and schedules.
Solution
Teknikum and Fellowmind initiated a comprehensive digital transformation project that extensively utilized the suite of applications in Microsoft Dynamics 365.
Why Fellowmind and Microsoft Dynamics 365
The strategic goal was to bring all the financial, operational and customer management processes to one unified platform. This would increase efficiency and provide an intelligent view of every aspect of the international and growing business.
"Fellowmind had strong evidence of similar previous change projects and a deep knowledge of all Microsoft Dynamics 365 solutions. Our timeline was strict, and Fellowmind convincingly demonstrated the effective integration of all project components," Matti Hulmi remarks on the criteria for selecting the partner.
The implementation of Dynamics 365 enabled the management of all functions from the same platform. This way, the processes and the data related to them could flow seamlessly throughout the sales, production and delivery chain. The scalable system is known for its smooth user experience and usability on any device. This was very important for a globally operating company.
The project consisted of several implementations, of which the most important were:
- A combined ERP and CRM system: Dynamics 365 Finance and Supply Chain Management (ERP) was integrated with Dynamics 365 Sales (CRM) solution to facilitate seamless operation chain and customer interaction. In addition, the asset management features for maintenance were integrated with the Power BI reporting tool as part of the comprehensive solution.
- Advanced inventory and production management: Dynamics 365 SCM was used to optimize inventory processes and production.
- Sales and sales management: Dynamics 365 Sales was integrated as part of the solution.
- Complete processes are complemented by ISV solutions such as Axtension (production planning), Exflow (purchase invoice processing), Nomentia (bank connections), and DAX, local solution for Hungarian economic reporting
- Azure Logic Apps integration solutions
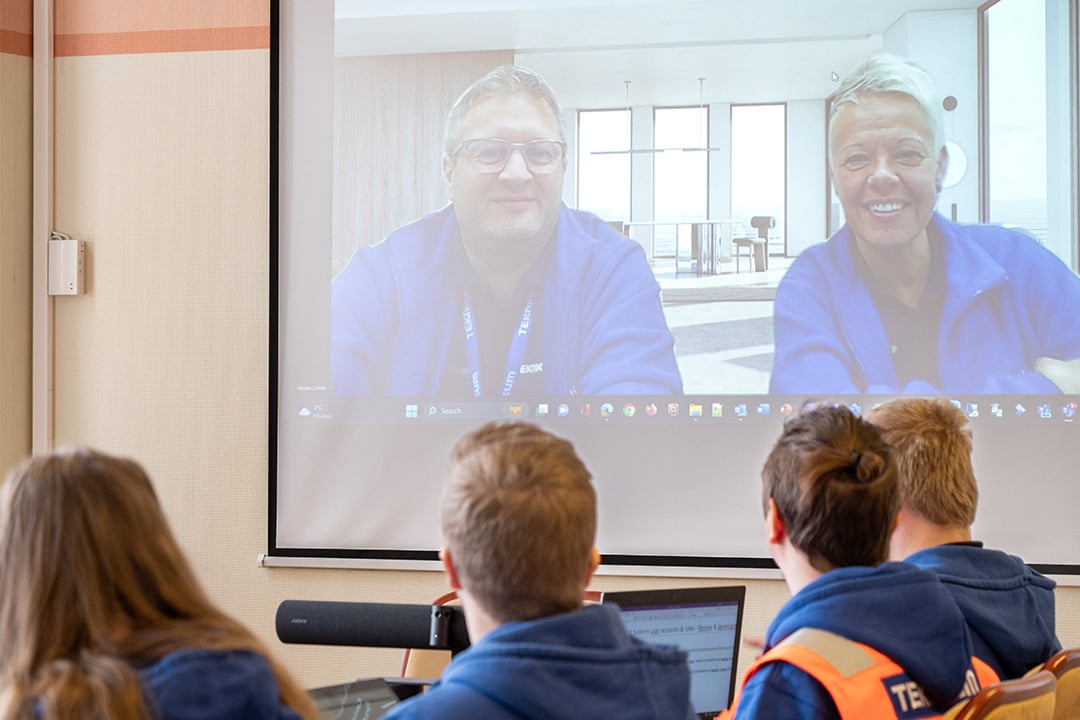
A global phased deployment with the Fellowmind Manufacturing Template delivery model
The solution was implemented using the Fellowmind Manufacturing Template delivery model, which reduced the time spent on the definition work and utilized the ready-made processes based on the best practices of the industry that the template brought. The project was phased so that a Global Template was first made, based on which the roll-out was brought to Teknikum's country units.
The systems were introduced in phases, first in Finland and then at the Hungarian factory. This also required organizing language training and strong change management to ensure that the system's use in English would succeed smoothly.
The goal was to do the project from person to person. Teknikum's CEO Jani Hämäläinen and ICT Manager Matti Hulmi, together with the Fellowmind team, ensured that people were committed to the change and understood why it was being done. The ICT Manager was present in Finland and Hungary and went through things with both the development team and the users. With consistent management, the project achieved its goals and stayed within the planned costs and schedules — despite the nuisance caused by the coronavirus.
The system offers increased transparency and promptness while gathering data that is analysed through Azure and Power BI. Predictive analytics enable more accurate strategic planning and creates competitiveness. Artificial intelligence is also used to streamline planning and operational activities.
"The new business platform takes us to the forefront of technology utilization. Innovation is the driver of Teknikum's growth and Dynamics 365 creates a modern foundation for it," says Matti Hulmi.
"Measurement and reporting took a big leap forward with the new system," says Jani Hämäläinen.
Our extensive product range requires a transparent system and transparent data to maintain organization. The new solution improves operational performance and customer service. Quality and accuracy are visible and felt in both customer and employee experience.
Results
As a result of the project, operational efficiency has increased and planning and forecasting have become more accurate: there is now a current overview of the whole business, enhanced profitability analysis, and detailed insights into sales and delivery status.
We manage our customers, products and processes much more precisely and better, which has improved our profitability. We have satisfied customers, and satisfied users. It is much more seamless to work with modern tools.
After the system implementation, automation has been increased with new Dynamics 365 functionalities and Power Platform tools, which have been used to implement, for example, several software robots.
There are also several value-added solutions in use, which have, for example, significantly improved the handling of purchase invoices, improved the accuracy of sales forecasts and provided a project management solution for project deliveries, which integrates seamlessly with the business platform.
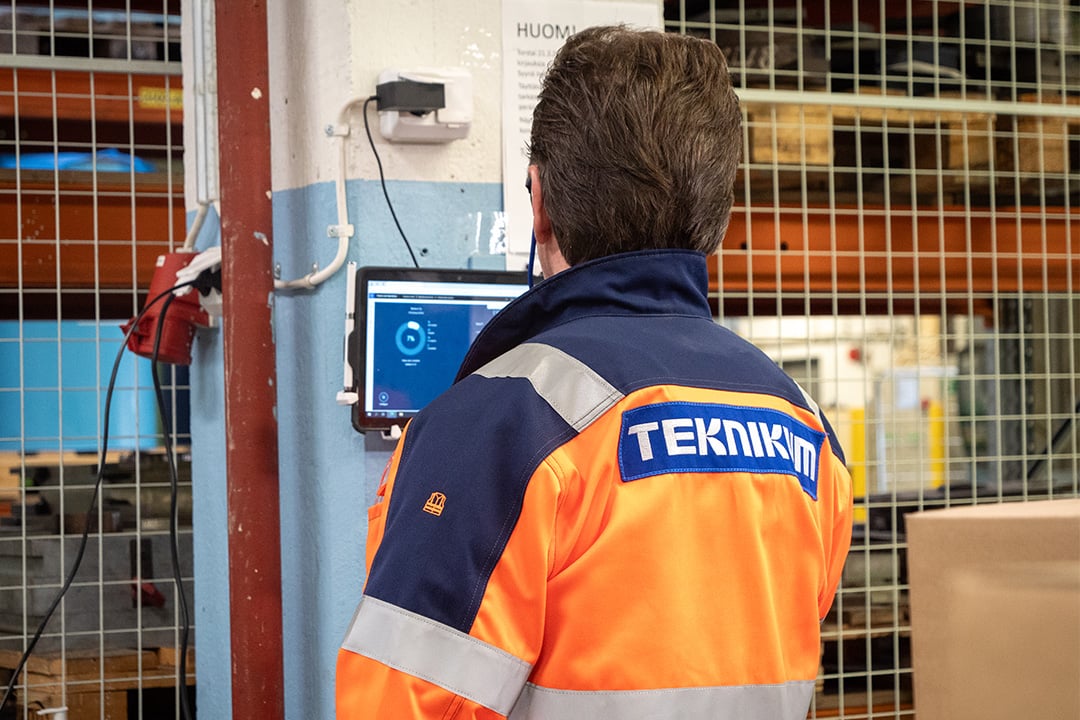
The new Dynamics 365 business platform supports the promotion of sustainability
Teknikum is committed to safety, responsibility and green transition. Eco-friendliness is one of the core values of the company, and it is ensured by operating in accordance with certified ISO management systems. The group has committed to reducing greenhouse gas emissions by 50% in phases 1-2 by 2030 and by 25% in phase 3 in the same time frame. The comprehensive solution built with Fellowmind supports the management and reporting of sustainability work both for the group's own use and for customer companies. In the future development of sustainable materials, the data and transparency provided by the Dynamics 365 platform throughout the product life cycle will be utilized.
With the new, unified business platform, Teknikum took a big step towards data-driven business. Combining the previous separate systems has significantly reduced complexity and improved efficiency in all functions.
We have the prerequisites with the new system to deliver the products on time, track them and manage the whole process from receiving the order to delivering the order on time and with the right quality. The data gives us opportunities to further develop our processes in the future.
Next on the roadmap is the wider use of artificial intelligence in operational activities and an investigation of the implementation of the Dynamics 365 Field Service solution to support field work. An IoT solution for the production and logistics process has also been considered. Business development is now done on top of a new holistic platform: this brings efficiency to the processes and enables innovative new types of services for customers in the future.
Fellowmind helped us take a big digital leap. We got support in change management and the project stayed nicely within budget and schedule.
Want to know more?
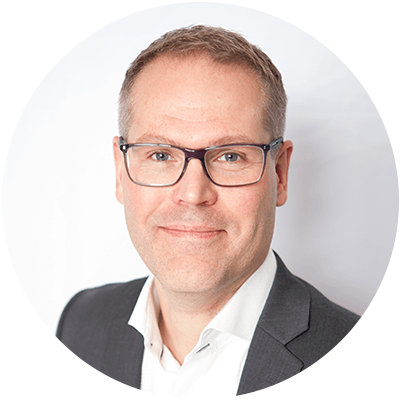
Tomi Tamminen
Vice President, Customer Experience
040 540 4687
tomi.tamminen@fellowmind.fi